-
Digital Twin and Digital Thread: Digital twin connects physical equipment and processes with its high fidelity simulation model replications in cyberspace using Industry Internet of Things (IIoT). Digital thread drives the smart manufacturing by advanced modeling and simulation tools that link product life cycle on concept-design-processing-manufacturing. Digital twin and digital thread are key enabling technologies for Smart Manufacturing and Industry 4.0. We have successfully deployed the digital thread and digital twin in design-analysis-manufacturing of the impellers.
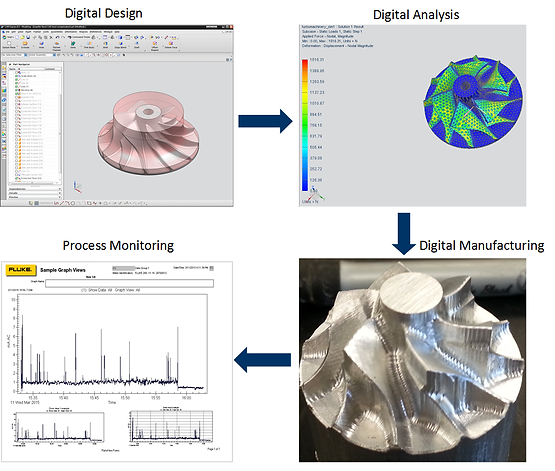
-
Friction stir welding (FSW): FSW is a solid state joining process. FSW has lower heat input and avoidance evasion of phase change during the welding process. FSW does not cause material phase change, resulting in minimum microstructural changes and better mechanical properties than conventional welding processes. FSW has been broadly used in aerospace, defense, shipbuilding industries. We have studied the donor material assisted high volume FSW processes.

-
Dynamic Data Driven Application Systems (DDDAS) for Manufacturing: DDDAS is an emerging powerful tool that allows more effective measurement processes to update the model. It brings challenges as well as opportunities for engineering applications on the aspects of mathematical algorithms, systems software, and data collection. We have successfully developed the DDDAS based applications on 1) digital twin for complex engineering products such as health management of aircraft engine, 2) cutting tool condition monitoring, 3) plasma spraying process, and 4) chemical mechanical planarization.

-
Cyber enabled sustainable manufacturing: The conventional product life cycle assessment is nontransparent to the manufacturing processes. The ASTM 60.13 E3012-16 standard brings new opportunities for quantitatively characterizing environmental aspects of manufacturing processes. We have successfully investigated simulation and experimental techniques to decide the unit manufacturing processes for CNC turning and milling.

-
Remote Diagnosis of PLC based Automated Manufacturing Systems: PLC-based manufacturing systems are typically discrete event systems characterized as event-driven and discrete input/output state space. For PLC based control, a critical issue is how to integrate intelligent monitoring and maintenance capabilities, including functions of monitoring, diagnosis, self-maintenance, and prognostics into the control system, thus ensuring the safety of operations and the quality of products. We have developed systematic approaches including sensor deployment, diagnoser, and architecture design for remotely detecting faults in PLC based automated systems.
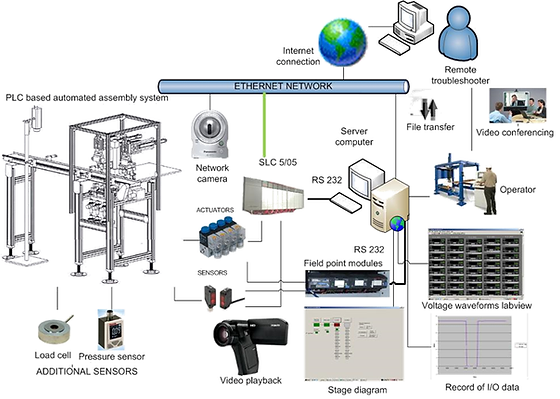
The research supports from NSF, ARO, ONR, NASA, VSU, CCAM, Sandvik Coromant, and Siemens are deeply appreciated!